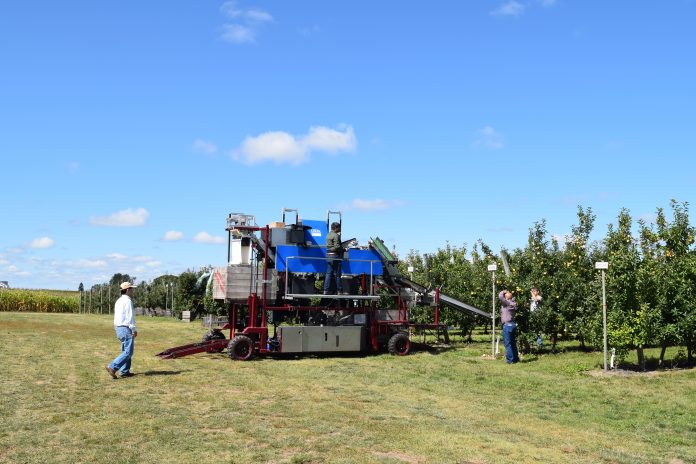
Over the last few years, big companies have invested millions of dollars for the development of commercial robotic apple harvesters. For instance, New Zealand based Abundant Robotics uses vacuum-based picking method while FFRobotics of Israel uses the robotic arm for apple collection. However, there are several challenges involved in harvesting of apples by robots, such as reaching the apples behind the leaves and picking the apples without damaging the fruit and the tree. These companies have demonstrated and developed prototypes, but it may take a couple of years to see a commercially available apple harvesting robot in the market. Therefore, as an intermediate solution, mechanical harvesting platforms are gaining prominence and are being widely used worldwide, where apple picking workers stand on moving platforms, collect and dump apples in bins. Research indicates that depending on the design and use, the harvest platforms can increase the labor efficiency by 15 to 60%.
Innovative infield sorting of apples
Infield sorting is an innovative approach of sorting apples in the filed on a moving harvest platform where only the fresh apples are sent to packing houses for storage, compared to hauling the good and bad apples in the same bin. Mixing of bad quality apples with the fresh apples increases chances of diseases during post-harvest storage. Economic analysis shows that on a 50-acre orchard with a yield of 50 bins for one acre with 10% bad quality apples, there could be around US$ 34,000 (approximately Rs 23,41,000 or 23.41 lakh) gross savings in post-harvest storage and packing if the bad apples were removed in the field. The USDA Sugarbeet and Bean Research Unit at Lansing, Michigan, USA working on the infield sorting of apples for the last few years has developed an innovative method of sorting (US patent 9,119,345 B1). Recently, the work was awarded the Rainbird engineering concept of the year award at the American Society of Agricultural and Biological Engineers (ASABE) annual international meeting 2019 in Boston, USA.
Harvest and infield apple sorting machine
The self-propelled apple harvest and infield sorting machine was first designed and developed in 2016, with the help of a commercial harvest equipment manufacturer. The machine serves both as a harvest aid platform as well an automatic sorting system for separating good and bad quality apples. Around six workers can stand on the platforms at different heights to collect apples from the ground, middle and top level heights. The collected apples are placed on conveyors to further send them to an onboard machine vision system (MVS). The MVS consists of a low-cost color camera, LED lighting in a closed enclosure. Apples are conveyed, singulated¹ and rotated for inspection under the camera. They are then tracked, identified and sorted automatically based on size and color into fresh and bad apples. The sorted apples are conveyed into different bins and filled automatically using the 3-bin fillers on the machine. Each bin filler movement in the bin is automatically controlled with the help of sensors. Each bin location on the platform and bin filler movement inside the bin is monitored using the distance and position sensors. Once the bins are filled, the automatic bin handling system replaces the filled bin with the empty bin. Automatic bin handling system consists of three sections of chain conveyors controlled by hydraulic motors, which are programmatically controlled for moving bins on the chain conveyor.
By: Anand Kumar Pothula, Research Fellow (Automation and Robotics) at University of Southern Queensland, Australia; Formerly he worked as a Postdoctoral Research Associate at USDA Sugarbeet and Bean Research Unit, Lansing, Michigan, USA
IndiFoodBev — authentic, impactful and influential
An English-language food and beverage processing and packaging industry B2B platform in print and web, IndiFoodBev is in its third year of publication. It is said that the Indian food and beverage industries represent approximately US$ 900 billion in revenues which implies more than 20% of the country’s GDP. Eliminating the wastage on the farmside can help to deliver more protein to a higher number of the population apart from generating sizable exports. The savings in soil, seeds, water, fertilizer, energy and ultimately food and nutrition could be the most immense contribution that country is poised to make to the moderation of climate change.
To improve your marketing and grow sales to the food and beverage processing and packaging industry, talk to us. Our research and consulting company IppStar [www.ippstar.org] can assess your potential and addressable markets in light of the competition. We can discuss marketing, communication, and sales strategies for market entry and growth.
Suppliers and service providers with a strategy and budget for targeted marketing can discuss using our hybrid print, web, video, and social media channels to create brand recognition linked to market relevance. Our technical writers are ready to meet you and your customers for content.
The second largest producer of fruit and vegetables in the world is continuously expanding processing capacities and delivery systems with appropriate innovative technologies. We cover product and consumer trends, nutrition, processing, research, equipment and packaging from farm to thali. Get our 2025 media kit and recalibrate your role in this dynamic market. Enhance your visibility and relevance to existing markets and turn potential customers into conversations. Ask for a sample copy of our bi-monthly in print or our weekly IndiFoodBev eZine each Wednesday.
For editorial info@ippgroup.in — for advertisement ads1@ippgroup.in and for subscriptions subscription@ippgroup.in
Naresh Khanna – 10 February 2025
Subscribe Now