The massive Interpack show took place in early May in Düsseldorf Germany. In the six-year gap since the last edition, packaging sustainability has become a central topic. At the show, 2,800 exhibitors, 140 thousand visitors – one-third being foreigners – and 18 halls were there to remind the importance of the sector. This is the first Interpack report from Cape Decision’s Dominique Huret for Packaging South Asia.
Packaging sustainability has become a concern for consumers and a headache for many brand owners whose sourcing and end-of-life scenarios for the packaging material have become decisive criteria. Then the major packaging producers also have net zero paths to achieve. The European regulations for all packaging in the EU to be reusable or recyclable in an economically viable way by 2030 in line with the EU Green Deal and the EU Circular Economy Action Plan are putting huge pressure on packaging manufacturers. Many companies of all sizes and across the whole value chain are sharing R&D and joining forces. Collaboration was and is not simply a buzzword.
(R)evolution in films and flexibles packaging
The trend toward mono-material remains obvious. Jindal Films displays its new PP mono-material to help replace PET-based laminates. The global leader in specialty showcased its BICOR OPP films designed to facilitate the switch from non-recyclable laminates (i.e. containing PET, alu-foil, paper …) towards mono-material mechanically recyclable PP-based laminates for flexible packaging markets.
The breakthrough technology the trademarked Bicor 12MB100, is a high stiffness OPP film with very low shrink for broad PET replacement applications to help brands in their ‘light-weighting’ journey. For more specialized applications when designing PP-based retort barrier laminates, Bicor 25MR100 and 25MR103 are being proposed as print outer webs. MR100 and MR103 were designed to help minimize the shrinkage and visual distortion during both the heat-sealing step and the steam autoclave sterilization step.
Since nothing beats a live demo, Jindal organized 11 industrial machinery partners for a live test using PP mono-material solutions on more than 20 packaging machines, covering the 4 commonly used flexible packaging formats. Most of these types of machines were typically previously running non-recyclable structures. These live demonstrations aim to prove the versatility of polypropylene films, with a balance of mechanical, barrier, optical, barrier, and heat seal properties unequaled by other materials.
Dow, Bobst, and Sun Chemicals collab for oneBarrier PrimeCycle
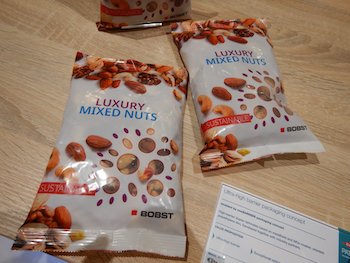
Photo Dominique Huret
Another ‘Design for recycling’ innovation for sustainable packaging is the oneBarrier PrimeCycle, a polymer-based mono-material developed by Bobst with several partners. PrimeCycle is an EVOH-free, topcoat-free solution for PE barrier films that offers a viable industrial alternative solution to metalized polyester films. It bears the advantage of being recyclable while retaining barrier qualities and performance equivalent to non-recyclable mixed-materials packaging structures, most notably metalized polyester film. Since September 2022, Bobst oneBARRIER PrimeCycle AlOx high barrier PE monomaterial packaging substrate has been certified with a recyclability level of 98% by the Germany-based Institute Cyclos – HTP.
Dow Packaging and Specialty Plastics, is the creator of the breakthrough technology while Sun Chemical, a global leader in the production of inks, coatings, and adhesives, is the developer of the adhesive for the oneBarrier PrimeCycle project and one of the co-creators of the primer. Bobst has opened its two huge demos and centers in Europe to all actors of the group to speed up industrial packaging solutions. Other films that are part of the oneBarrier project, including the FibreCycle solutions relating to recycle-ready high barrier paper/fiber-based packaging have already been stepped up from R&D solutions to industrialized solutions, while work is also underway for the development of compostable and biodegradable packaging substrates.
Sabic and Covestro’s Truecircle solutions
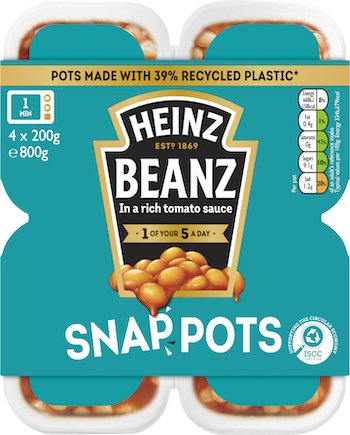
Photo Dominique Huret
A pioneer in the industry back in 2019 at Davos, Sabic started the building of a small-scale commercial unit to produce certified circular polymers from the advanced recycling of used plastics. Since then, Sabic has been employing existing facilities to process smaller volumes of advanced recycled materials for brand owners and customers for a variety of applications already available in the market. At Interpack, Sabic showcased its Trucircle solutions for flexible packaging and in particular heat resistant mono-PE pouches for products that need to be heated in the microwave.
Done in close cooperation with Covestro, this new fully recyclable stand-up pouch is made with Sabic BOPE material including Covestro’s heat-resistant coating resin technology. The transparent coating, currently in a trial phase, has been tested and validated, offering a broader sealing temperature window when processing on form, fill and seal lines for flexible packaging as it prevents both film shrinkage and film sticking to heat seal bars during FFS. Sabic’s BOPE material is available in certified circular and renewable grades.
“Sabic has a target of one million metric tons of Trucircle solutions by 2030 and this intends to help usher in the new circular economy. Driving circularity for plastics will require a rapid transformation of the entire value chain, which is only possible through collective action, innovation, and collaboration across the industry and ecosystem of waste management. Therefore, we are working hard with downstream and upstream partners to accelerate this process,” said Abdulrahman Al-Fageeh, Sabic CEO.
Early this year, Sabic launched a flow pack of biaxially oriented recycled polypropylene (BOPP) for the KIND fruit bar from manufacturer Mars. The material is produced from a post-consumer recycled mixed plastic waste stream, then converted into pyrolysis oil, and transformed into granulate approved for food contact by Sabic. This is then delivered to Taghleef, which turns it into the foil. A polymer converter finally uses the BOPP film to produce printed packaging for Mars fruit bars.
BOPP as packaging material for pet food packaging is not new for Mars but for human food contact is another step forward. A few days after the fair, Sabic announced a sector initiative. Together with BASF, Covestro, Dow, LyondellBasell, Mitsubishi Chemical, Sabic, and Solvay, they have committed to join R&D projects towards more sustainable plastic waste processing and mechanical and chemical recycling.
Constantia Flexibles Ecolutions

Photo Dominique Huret
Constantia Flexibles could not be missed on the fairground. The company’s motto was to offer a 360-degree material approach for the pharma and consumer business under their product range Ecolutions. No less than thirty machine suppliers collaborated with them to demonstrate several of their solutions. First, the EcoLam laminates, based on PE compounds are designed to replace non-recyclable laminates like PET/PE, polyamide/PE, and PET/Alu/PE. “Several characteristics make the mono PE laminate EcoLam more sustainable and efficient than other products in its league – they are lighter than others, have a solid thermal resistance, and use a lower barrier polymer content due to the combination of processes and resins. Another advantage of the EcoLam range is that its barrier properties can be customized to the product. All EcoLam grades are certified by RecyClass and are compliant with all existing sorting and recycling technologies commonly used at an industrial scale in Europe.
“Interpack is the opportunity for us to collaborate with 30 machine suppliers and demonstrate the capabilities of our materials,” said Marc Rademacher, executive vice president of Consumer Commercial at Constantia. EcoVer is Constantia Flexibles’ mono polypropylene (PP). It is proposed in different barrier grades – EcoVer, EcoVerPlus, and EcoVerHighPlus. Applicable on form, fill and seal vertical and horizontal machines, with high transparency, low initial sealing temperatures, heat resistance, and good stiffness. This allows their use for beverages, snacks, dairy, confectionery, home, and personal care (HPC), pet care, or processed food. EcoVer, a PP mono structure, is recyclable in the mixed PO stream. Two of Constantia Flexibles’ solutions for lids were also on display on some equipment. The company aims at being the market leader in lidding.
IndiFoodBev — authentic, impactful and influential
An English-language food and beverage processing and packaging industry B2B platform in print and web, IndiFoodBev is in its third year of publication. It is said that the Indian food and beverage industries represent approximately US$ 900 billion in revenues which implies more than 20% of the country’s GDP. Eliminating the wastage on the farmside can help to deliver more protein to a higher number of the population apart from generating sizable exports. The savings in soil, seeds, water, fertilizer, energy and ultimately food and nutrition could be the most immense contribution that country is poised to make to the moderation of climate change.
To improve your marketing and grow sales to the food and beverage processing and packaging industry, talk to us. Our research and consulting company IppStar [www.ippstar.org] can assess your potential and addressable markets in light of the competition. We can discuss marketing, communication, and sales strategies for market entry and growth.
Suppliers and service providers with a strategy and budget for targeted marketing can discuss using our hybrid print, web, video, and social media channels to create brand recognition linked to market relevance. Our technical writers are ready to meet you and your customers for content.
The second largest producer of fruit and vegetables in the world is continuously expanding processing capacities and delivery systems with appropriate innovative technologies. We cover product and consumer trends, nutrition, processing, research, equipment and packaging from farm to thali. Get our 2025 media kit and recalibrate your role in this dynamic market. Enhance your visibility and relevance to existing markets and turn potential customers into conversations. Ask for a sample copy of our bi-monthly in print or our weekly IndiFoodBev eZine each Wednesday.
For editorial info@ippgroup.in — for advertisement ads1@ippgroup.in and for subscriptions subscription@ippgroup.in
Naresh Khanna – 10 February 2025
Subscribe Now