The UFlex Cylinder Division in Noida is well-known as a trusted manufacturer of rotogravure printing cylinders for flexible packaging. Although the division’s capabilities extend from gravure printing cylinders to flexo plates and flexo printing sleeves, it is still the leader in automation and the capability of producing cylinders for water-based gravure using its Think Labs robotic engraving system.
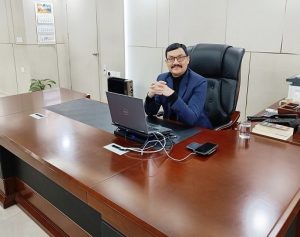
On our visit to the UFlex Cylinder Division in Noida, we met with Parwez Izhar, chief executive officer of cylinder business and senior vice president at UFlex, who showed us the plant and explained the working of the gravure aspect as well as the addition of the new Kodak Flexcel NX system which modernizes and expands the division’s flexo platemaking capabilities and capacity. The company’s strength comes from upgrading and acquiring the latest technology to meet the most critical demands of its customers.
The cylinder division’s gravure engraving capabilities include both the electro-mechanical engraving lines and the Think Labs robotic laser engraving line. In the robotic laser engraving line or system, robots do the entire process of preparing, engraving, and finishing the cylinders in a special air-conditioned and dust-proof enclosure controlled by the technical staff using the digital files sent by the prepress team. The process of engraving and finishing is entirely automated while the programming or instructions and specifications for each cylinder are provided by the technical staff.
The robotic engraver is more productive and sustainable
By comparing the preparation of cylinders in both manually and by the robotic system, we learned that the VOC levels of the robotic engraving line section are 25-30% less than the electro-mechanical section, making it healthier and more sustainable. Moreover, in the robotic engraving line, the energy-saving and efficiency are higher, the cylinder life is better, and the system needs less manpower.
At the same time in gravure printing with cylinders with cell patterns that use less ink while maintaining high quality which makes customers happy with the results and the savings. Currently, the single robotic line can produce 80 cylinders daily, whereas with the cylinder division’s multiple electro-mechanical engravers can produce 250 cylinders daily.
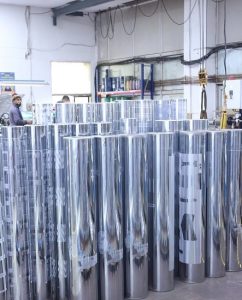
Izhar spoke about the trends for modernization in gravure, “Customers in the flexible packaging industry prefer the cylinders with low gsm or low ink consumption. We also use make gravure cylinders for printing with water-based inks, so that the VOCs are low and eco-friendly. This brings our customers and us closer to the sustainability goals. Today, the trend is for the use of water-based inks in gravure, and we are the best in producing the cylinders for printing with water-based gravure inks as we use the Think Lab robotic engraving line to produce them.” Increasingly, UFlex’s packaging division and converter customers of the cylinder division are engaged in the trend for gravure printing with water-based gravure inks.
Izhar concluded our conversation by commenting on the company’s achievements during the Covid-19 pandemic, saying, “When the second wave of the pandemic hit India, we faced many challenges as our operations and the supply chain was affected. We were unable to get the base shells, which are the raw material for cylinder making. As there was a shortage of oxygen cylinders, we informed our manufacturing units to buy plasma arc cutting machines. Our capacity was compromised, and that’s why Q1 was not good for us, but as the situation improved, we made record sales in Q2 and Q3. The reason is that Covid-19 increased the demand for packaging, so we were able to produce more engraved cylinders.”
IndiFoodBev — authentic, impactful and influential
An English-language food and beverage processing and packaging industry B2B platform in print and web, IndiFoodBev is in its third year of publication. It is said that the Indian food and beverage industries represent approximately US$ 900 billion in revenues which implies more than 20% of the country’s GDP. Eliminating the wastage on the farmside can help to deliver more protein to a higher number of the population apart from generating sizable exports. The savings in soil, seeds, water, fertilizer, energy and ultimately food and nutrition could be the most immense contribution that country is poised to make to the moderation of climate change.
To improve your marketing and grow sales to the food and beverage processing and packaging industry, talk to us. Our research and consulting company IppStar [www.ippstar.org] can assess your potential and addressable markets in light of the competition. We can discuss marketing, communication, and sales strategies for market entry and growth.
Suppliers and service providers with a strategy and budget for targeted marketing can discuss using our hybrid print, web, video, and social media channels to create brand recognition linked to market relevance. Our technical writers are ready to meet you and your customers for content.
The second largest producer of fruit and vegetables in the world is continuously expanding processing capacities and delivery systems with appropriate innovative technologies. We cover product and consumer trends, nutrition, processing, research, equipment and packaging from farm to thali. Get our 2025 media kit and recalibrate your role in this dynamic market. Enhance your visibility and relevance to existing markets and turn potential customers into conversations. Ask for a sample copy of our bi-monthly in print or our weekly IndiFoodBev eZine each Wednesday.
For editorial info@ippgroup.in — for advertisement ads1@ippgroup.in and for subscriptions subscription@ippgroup.in
Naresh Khanna – 10 February 2025
Subscribe Now